1000 metres in a
Single Blow
HFCL's Optibend Unitube Mini
Cable for FTTx Connectivity
Case Study
Highlights
Designed for
single-blow
installations
exceeding 1000 m
26 distinct
Variants
developed to meet diverse
customer requirements
Cables
available from
2 fibers to
36 fibers
The Optibend Unitube Mini Cable covers
1000 m in only 15 minutes*
New S-Z shaped jetting test track engineered to simulate actual field conditions
Background
HFCL faced a significant challenge when a European customer requested a high-performance FTTx solution. The task was to develop a Unitube blown cable capable of reaching 1000 metres in an 8/5 mm microduct at 7 bar duct pressure. Although promising in early tests, the initial 24 fibers cable prototype underperformed in the field when faced with stringent field conditions. This setback motivated and provided an opportunity for HFCL to optimize its design. Through 26 iterations and extensive testing, HFCL collaborated with HTL Hosur to develop an Optibend Unitube Mini Cable with a low-friction outer jacket. Validated by rigorous simulations and field-like tests, the final design achieved outstanding performance, effectively meeting the customer's demands.
Customer’s Overview
HFCL was approached by a prominent European telecommunications leader known for its forward-thinking approach to infrastructure, seeking customized cable solutions. Operating in a highly competitive industry, they have consistently pushed the boundaries of technology to deliver superior connectivity solutions. Recently, they made headlines with their ambitious plans to expand high-speed internet access across rural and urban areas, demonstrating their commitment to advancing telecom services.
Despite their successes, the customer faced significant challenges in optimizing FTTx installations within smaller microducts. There were limitations during field installation due to approximately 7 bars of available duct pressure. The cable had to be blown through a distance of up to 1000 metres in a single attempt, navigating through turns, undulations, and changes in elevation along the route.
Recognizing the need for a more effective solution, they sought a partner known for innovation and reliability. They chose to collaborate with HFCL, driven by our proven track record in providing cutting-edge cable solutions and our commitment to customer-specific customization. Our expertise and state-of-the-art facilities promised a solution that would not only meet but exceed their performance expectations.
Challenges Faced
Material Innovation
Outer jacket compound required minimizing friction for maximum blowing distance. After extensive experimentation, we have devised 4 different jacket compounds, each combining different base resins and anti-slippage additives. Notably, the final one emerged as the top performer. This process of compound development was not without its challenges, spanning approximately six months to pinpoint the optimal composition for this specific application.
Engineering Complexity
Developing a unitube blown cable tailored for FTTx applications, intended for installation within 8/5 mm microducts spanning a distance of 1000 metres, while adhering to a strict maximum duct pressure limit of 7 bars.
Initial Performance Gap
Our cable design fell short during field testing, managing only 150 metres compared to a competitor's cable reaching 1000 metres effortlessly.
Iterative Design Process
Balancing cable stiffness was critical, too stiff hindered smooth navigation, while too flexible caused buckling.
HFCL’s Approach to the Challenges
Facing the challenge of optimizing FTTx installations in smaller microducts, HFCL approached the task with determination and innovation.
-
1
Identification of Initial Solution
HFCL responded to the customer's demand with a recently developed 24 fibers cable, showcasing compatibility for blowing into the requested duct size. Despite initial promise, field testing revealed shortcomings, inspiring us to strive for improvement.
-
2
Commitment to Improvement
Collaborating with the HTL Hosur team, we meticulously refined both the cable design and outer jacket material composition, testing almost 26 different variants to achieve the desired outcome.
-
3
Thorough Testing and Validation
The cable underwent trials on the standard IEC Nx100 track, validating cable performance as per industry standards. Furthermore, we designed and constructed a new S-Z shaped test track to establish the most rigorous testing conditions possible, simulating real-world conditions and intentional bends in the test route.
-
4
Focus on Design Optimization
Recognizing the importance of stiffness in navigating intricate bends, HFCL optimized the cable design to ensure smooth movement without compromising flexibility. This approach ensured efficient installation even in challenging FTTx topologies.
-
5
Innovation in Material Development
Understanding the critical role of low-friction properties in blowing distance, HFCL's HTL Hosur renowned for their expertise in developing customised polymer material compounds developed an outer jacket compound with exceptional low-friction characteristics, enhancing the cable's performance significantly.
-
6
Successful Qualification and Validation
Understanding the critical role of low-friction properties in blowing distance, HFCL's HTL Hosur renowned for their expertise in developing customised polymer material compounds developed an outer jacket compound with exceptional low-friction characteristics, enhancing the cable's performance significantly.
Success Metrics
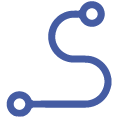
Achieved 1000 m Blowing Distance
Our optimized Optibend Unitube Mini Cable design resulted in a groundbreaking 1000 metres blowing distance, significantly surpassing initial field performance and demonstrating our ability to meet and exceed customer expectations.
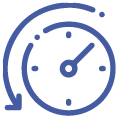
Reduced Blowing Time by Two-Thirds
Leveraging enhanced stiffness and low-friction outer jacket material, we achieved a remarkable 15-minute blowing time for the full 1000 metres, one-third of the time required by the competitor’s cable.
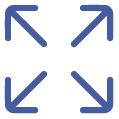
Developed 26 Design Variants
To achieve the final optimized design, we developed and tested 26 different variants, showcasing our commitment to innovation and customer-specific customization to deliver superior performance. We ensured that the cables maintained the same dimensions without compromising any mechanical and environmental performance.
Result
We proudly introduce the Optibend Unitube Mini Cables- the slimmest cabling solution available, ranging from 2 fibers to 12 fibers with a diameter of approximately 2.1 mm. Additionally, they are suitable for microduct air-blown installations and can accommodate up to 36 fibers with a diameter of approximately 2.4 mm.
-
"Thanks to HFCL's groundbreaking cable design, we achieved a remarkable 1000 metres blowing distance in just 15 minutes – a feat that surpassed our expectations threefold. This unparalleled performance has not only streamlined our FTTx installations but has also given us a competitive edge in the market.” - Our Customer
*Disclaimer: The observed test result at the customer site cannot be guaranteed for every route type.
About HFCLHFCL is a leading technology company specializing in creating digital networks for telcos, enterprises, and governments. Over the years, HFCL has emerged as a trusted partner offering sustainable high-tech solutions with a commitment to providing the latest technology products to its customers. Our strong R&D expertise coupled with our global system integration services and decades of experience in fiber optics enable us to deliver innovative digital network solutions required for the most advanced networks.
The company’s in-house R&D Centres located at Gurgaon and Bengaluru along with invested R&D houses and other R&D collaborators at different locations in India and abroad, innovate a futuristic range of technology products and solutions. HFCL has developed capabilities to provide premium quality Optical Fiber and Optical Fiber Cables, state-of-the-art telecom products including 5G Radio Access Network (RAN) products, 5G Transport Products, Wi-Fi Systems (Wi-Fi 6, Wi-Fi 7), Unlicensed Band Radios, Switches, Routers and Software Defined Radios.
The company has state-of-the-art Optical Fiber and Optical Fiber Cable manufacturing plants in Hyderabad, an Optical Fiber Cable manufacturing plant in Goa, and its subsidiary HTL Limited in Chennai.
We are a partner of choice for our customers across India, Europe, Asia Pacific, the Middle East, Africa, and the USA. Our commitment to quality and environmental sustainability inspires us to innovate solutions for the ever-evolving customer needs.