Feeling lost in a maze of fiber optic cables? Understanding the differences between central core ribbon and loose tube fiber cables is crucial for making the right choice for your project.
The two major types of fiber cables, central core ribbon and loose tube cable, have been prevalent in the telecommunications industry for several decades now. The selection between the two main types of fiber cables, based on their characteristics and the specifics of the application, is crucial to the success of the fiber deployment as well as future performance.
What are Loose Tube Fiber Cables?
Loose tube fiber cables were initially developed in the 1970s and made fiber installations possible by protecting fragile optical fibers from the stress of installation. A small, hollow plastic tube containing multiple fibers is the basic building block of these cables. One or more of these tubes are wound around a central strength member and enclosed in a jacket, with optional armoring. This results in a compact cable structure that easily scales to high-fiber counts. With the use of water-blocking gel or dry superabsorbents, loose tube fiber cables provide long-term protection from environmental moisture.
The loose tube design family continues to be used in outdoor environments across all geographies. The combination of twisted tubes and a rigid, load-carrying central strength member offers protection from high pulling tensions, making it a perfect option for installations in challenging outdoor plant environments. Compared to central tube cables, loose tube fiber cables are more flexible and have a lower minimum bend radius, making it easier to store cable slack for later splicing or customer connection. Perhaps the biggest benefit of loose tube cable is convenient mid-span access. The multi-tube structure allows for easy access to individual fibers within one tube without disturbing the others.
What are Central Core Ribbon Fiber cables?
Central core ribbon fiber cables first emerged in the 1990s. An optical ribbon consists of multiple colored fibers arranged in a row and held together by an adhesive. Common fiber counts for ribbons include 8, 12 or 24 optical fibers joined together. The use of ribbons allows the design of compact optical cables, as multiple ribbons can be brought together into a stack or bundle in the middle of a central core cable. High fiber counts allow for a higher density of optical fibers within a smaller diameter cable than what is possible with equivalent loose tube cables. Central core ribbon cables generally include reinforcing strength members embedded within the outer jacket, which can result in a relatively high bend radius.
The most significant advantage offered by central core ribbon cables is realized after they have been installed. Ribbons enable mass fusion splicing, allowing multiple fibers to be joined together in one splicing operation, accelerating network deployment. As shown below, compared to loose fiber cables, ribbons can allow up to an 85% reduction in splicing time. Mass fusion splicing of ribbons also ensures faster network restoration in case of a disruption. These features make it ideal for high-density data center applications, backbone and metropolitan ring connections, and situations where space is limited.
The productivity benefit enabled by mass fusion splicing of central core ribbon fiber optic cables is one of the reasons for their popularity over the last three decades. The global ribbon fiber optic cable market is likely to reach $7,623.2 million by 2030, up from $2,834.6 million in 2021, according to Report Ocean.
Comparing Central Core Ribbon and Loose Tube Fiber Cables:
Both central core ribbon and loose tube fiber cables have been widely adopted by the telecom industry, especially for outdoor deployments in all parts of the world. The key difference between the two is how the individual fibers are organized: bonded together in ribbons but unconnected within small tubes in a loose tube.
Traditional central core flat ribbon cables offer several advantages, particularly for high-density applications. A flat structure with multiple fibers grouped allows for fast mass fusion splicing, during both installation and restoration. The high density of high fiber count central tube ribbon cables allows service providers to maximize fiber count within ducts or other restricted spaces. However, there are some limitations to central core ribbon cables. Most notably, midspan access to fibers in a central core cable is complicated, as the entire core of the cable must be exposed even if access to only one individual fiber or ribbon is needed. With strength members embedded in the outer jacket, central core ribbon cables can be easier to crush and kink than loose tube cables. Finally, mass fusion splicing machines are more expensive than single-fiber splicing machines.
Loose tube cables have their own benefits and drawbacks. Unlike central core ribbon cables, midspan access is easy, since a splicing technician generally only needs to access one of the tubes. Loose tube cables tend to have a lower bend radius, allowing the use of smaller slack coils, vaults, and pedestals. The biggest drawback of traditional loose tube cables is the time required for individual splicing of loose fibers one by one. Last but not least, single-fiber splicing machines are relatively inexpensive.
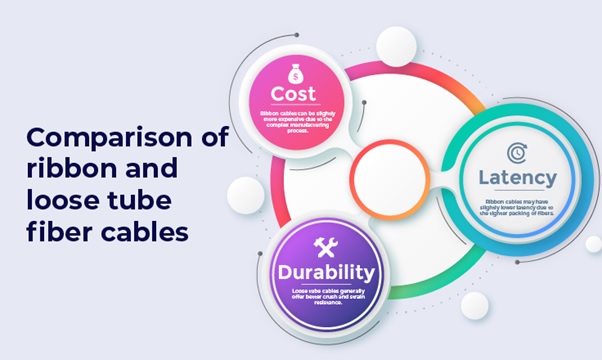
How IBR Addresses Some of the Limitations of Traditional Flat Ribbon Cables
The recent development of Intermittently Bonded Ribbons (IBR) addresses some limitations of traditional flat ribbon cables. In flat ribbons, the fibers are completely encased in adhesive, forming a solid 2-D structure. The ribbons in IBR cables can be thought of as flat ribbons in which 80% of the adhesive has been removed, with intermittent adhesive joints between adjacent fibers. Outside of a cable, intermittently bonded ribbons take on a flat shape that supports conventional mass fusion splicing. However, within cables, the intermittent bonds allow the IBRs to bend and flex, allowing the ribbons to completely occupy the space within a central core cable, approximately doubling the fiber packing density relative to flat ribbon cables. This is especially beneficial at low fiber counts, where the packing of flat ribbons within round cables is inefficient. Another benefit of IBR is its much easier handling in closures, vaults, and pedestals. Traditional flat ribbons have a large bend radius and a “preferential bend”, meaning they can only be bent in one direction, while IBRs can twist and flex, allowing a smaller bend radius and even enabling the use of smaller, lower-cost closures.
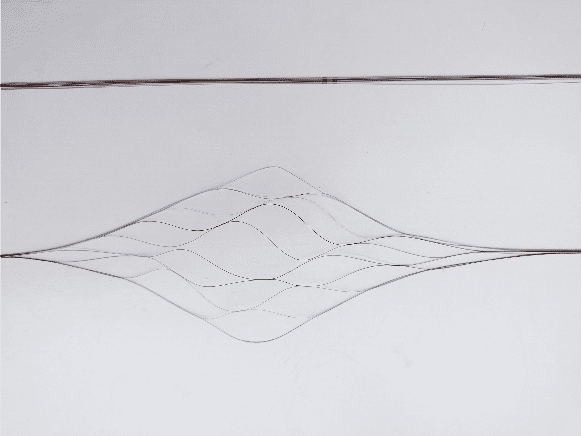
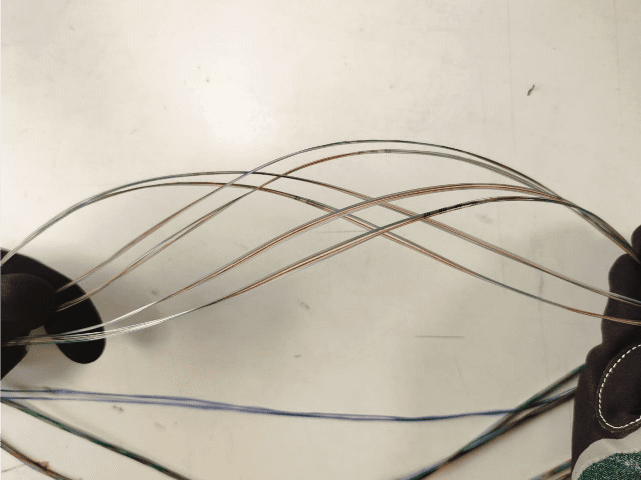
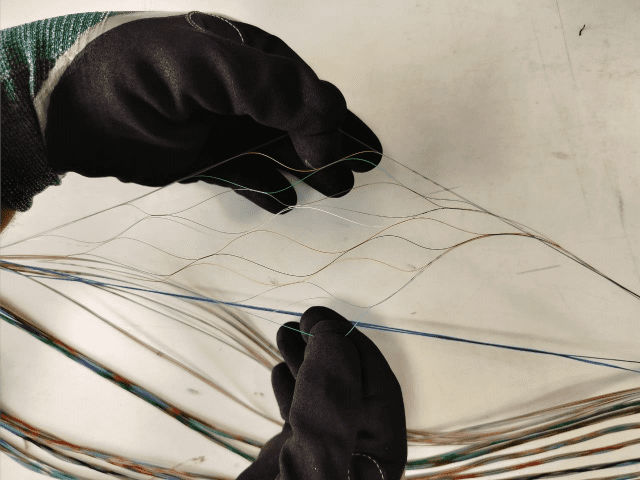
Splice time comparison: IBR vs. loose fibers
Research was conducted to compare the time required to splice IBR ribbons as compared to splicing individual fibers in a loose tube microcable. Specifically, the study compared the splicing time for 12 individual fibers in a loose tube with mass fusion splicing of a 12-fiber IBR Ribbon.
The following steps need to be carried out for each fiber for the loose tube fibers:
- Removal of the plastic jacket.
- Cleaning the water-blocking gels over the fibers.
- Removing the coating on the fibers.
- Splicing and protecting the splice point with a protective tube.
Jacket removal is needed for IBR cables as well. However, after that, the IBR ribbons only need cumulative stripping of the coating, cleaving the tip of fibers, mass fusion splicing of 12 fibers at once, and protecting the splice point with a heat shrink tube.
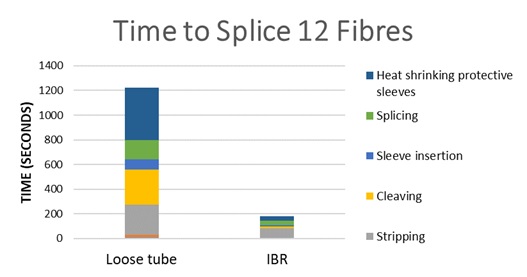
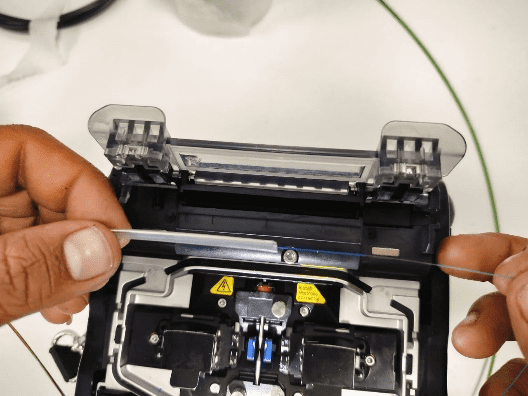
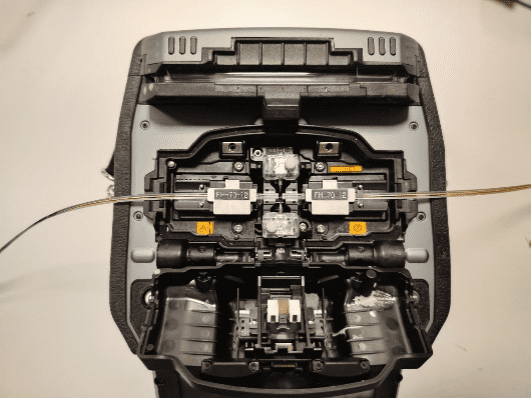
Based on this comparison, we can calculate that it takes approximately 12 hours to splice all the fibers in a 432-fiber loose tube cable, whereas a 1728-fiber IBR Duct Cable can be spliced in 7¼ hours: four times as much fiber spliced in 40% less time!
While traditionally, only one type of cable is used in a network, this is now changing as customers’ demands are becoming more complex and bandwidth requirements continue to skyrocket. Increasingly, a combination of ribbon and loose tube fiber cables is being used in the same network. This can be beneficial in fiber-to-the-home or fiber-to-the-antenna networks: ribbon cables can be used for high-capacity trunks and metropolitan rings, while loose tube cables can be used for close-to-the-user distribution, where frequent mid-span access to connect customers is often required.
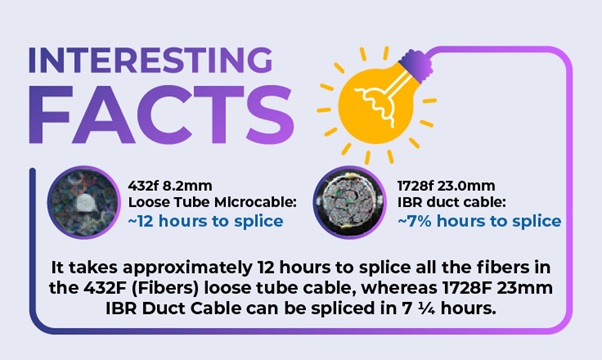
In Closing
Suffice to say that there is no one-size-fits-all solution. The decision to deploy ribbon optical cable or loose tube optical cable depends on several factors, including network design, splicing, and deployment costs, among others. Ribbon optical cable provides high packaging densities for high fiber count cables, making them perfect for deployment in constrained space. In addition, their mass fusion splicing capability means that they enable significant cost and time savings in trunk networks. Loose tube cables are potentially a better choice for networks where frequent mid-span access to connect drop cables is required, such as FTTH distribution networks.