In today's digital world, having reliable connections is key for smooth network systems. Fiber splice joint closures are vital but often overlooked. It plays a crucial role in keeping networks running smoothly, even in the harshest conditions. Let’s explore what they are, why they matter, and how technological advancements are making them even better.
Understanding Fiber Splice Joint Closures
Fiber splice joint closures are key in fiber optic networks. They protect and keep spliced fiber optic cables in good shape. Knowing what a fiber splice closure is helps us see its vital role in keeping connections safe from harm. This is crucial for keeping data transfer reliable in many systems
Components of a Fiber Splice Joint Closure
The parts of joint closures work together to keep things stable and reliable. Key parts include:
Component | Function |
---|---|
Enclosure | Protects against environmental hazards |
Splice Trays | Organizes and secures spliced fibers |
Sealing Mechanisms | Prevents moisture and dust ingress |
Strain Relief | Minimizes stress on fiber connections |
Importance of Joint Closures in Network Infrastructure
1. Protection Against Environmental Factors
Fiber optic networks are vulnerable to the elements, especially in outdoor or rugged installations. Joint closures are equipped with IP-rated seals (like IP68), offering exceptional protection against rain, dust, UV rays, and extreme temperature fluctuations. This protection ensures that the network continues to perform reliably, whether in scorching heat, cold, or humid conditions.
2. Durability and Long-Term Reliability
Fiber optic infrastructure is designed to last for decades, but without reliable protection, that longevity could be at risk. High-quality joint closures are built to endure, significantly reducing the need for ongoing maintenance and minimizing network downtime. Their durability ensures consistent performance over time, which is essential for minimizing operational disruptions and keeping service costs low.
3. Maintaining Signal Integrity
The integrity of data signals is crucial to network performance. Any disruption or degradation in the fiber splice can lead to signal loss, which could impact everything from fiber-to-the-home (FTTH) installations to high-speed networking. Fiber splice joint closures ensure that the fiber splices are securely protected, reducing the chances of signal interference and maintaining the highest quality of service.
4. Future Readiness and Scalability
As the demand for faster and more reliable networks continues to grow, so does the need for scalable solutions. Many modern joint closures feature modular designs, making it easy to add more fibers, upgrade systems, or expand network capabilities without extensive rework. These flexible designs ensure that the network can grow and adapt over time.
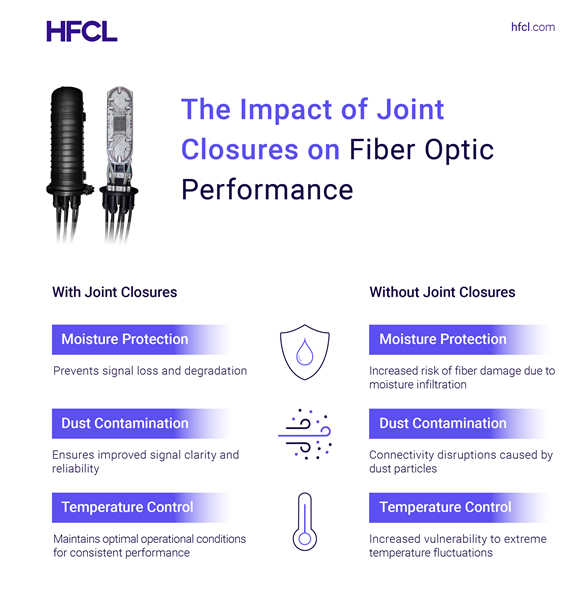
Types of Fiber Splice Joint Closures
At HFCL, we understand that different installations have different requirements. Our range of fiber splice joint closures caters to a variety of deployment scenarios, from residential installations to complex industrial applications.
1. Dome Type Fiber Splice Closure
HFCL’s dome-type closures are constructed from high-grade polypropylene (PP), offering excellent UV resistance and reusable seals. These closures provide secure fiber splicing for distribution networks, ensuring long-term durability and ease of access.
-
• Mechanical Type:
Utilizing heat-shrinkable materials, these closures provide a moisture-proof seal, making them ideal for underground installations where environmental factors are more aggressive.
Use Cases: Transportation Networks, Distribution Networks, CATV Systems -
• Heat Shrink Type:
These closures are secured using screws or clamps, making them quick and easy to access for maintenance. They are well-suited for aerial, underground, or direct-buried fiber splices.
Use Cases: CATV Applications, Pressurized Cable Installations, General Outdoor Use
2. Inline Type Fiber Splice Closure
HFCL’s inline closures are made from anti-corrosive polycarbonate, making them suitable for a variety of installations, including aerial, underground, and direct-buried settings. These closures are especially effective in providing long-lasting protection for fiber splices in tough environments.
Use Cases:- • Aerial Network Installations: Protects fiber splices from exposure to environmental factors and mechanical stress.
- • Direct Burial Applications: Designed to withstand soil pressure and moisture in underground deployments.
- • FTTH Access Networks: Secure and durable splicing for fiber-to-the-home access points.
Installation of Joint Closures
Proper installation of fiber splice joint closures ensures the long-term performance and reliability of networks. The process begins with thorough site preparation and follows a structured step-by-step approach.
1. Site Preparation
Before installation, it’s vital to prepare the site properly:
- • Assess Environmental Factors: Evaluate the weather conditions and geography to determine any potential challenges for installation.
- • Select a Suitable Location: Choose a spot that is accessible for maintenance and protected from extreme weather or physical damage.
- • Gather Materials and Tools: Ensure all necessary components are available, including the closure, splice trays, sealing tools, and splicing equipment.
2. Step-by-Step Installation Guide
Follow these steps to ensure a robust and reliable closure setup:
- • Prepare the Site: Secure any required permits and organize the workspace to ensure safety and efficiency.
- • Open the Closure: Carefully open the splice closure and arrange the splice trays as per the manufacturer’s instructions.
- • Insert Fiber Cables: Route the fiber cables into the closure, ensuring proper alignment and organization to avoid tangling or damage.
- • Perform Fiber Splicing: Splice the fibers according to the manufacturer's guidelines, ensuring minimal signal loss.
- • Seal the Closure: Assemble the closure, ensuring all gaskets and seals are properly installed to provide a watertight and airtight seal.
- • Test and Verify: Check the installation using tools like an OTDR to confirm the integrity and performance of the splices before finalizing.
Step | Action Required | Key Considerations |
---|---|---|
1 | Site Preparation | Identify environmental challenges |
2 | Confirm Location | Access and protection from elements |
3 | Gather Tools | Check for completeness and functionality |
4 | Install Closure | Follow specification guidelines |
5 | Conduct Testing | Ensure performance criteria are met |
How Technology is Shaping the Future of Fiber Splice Joint Closures
At HFCL, we’re not just focused on meeting today’s requirements; we’re shaping the future of network infrastructure. Through our subsidiary HTL Ltd in Chennai, we’re leading the charge with technological innovations that enhance the performance of fiber splice joint closures.
1. Advanced Materials
Our closures are crafted from high-performance polymers that resist UV rays, chemicals, and physical impacts. These materials ensure our closures maintain their protective qualities over time, even in the most demanding conditions.
2. Improved Sealing Techniques
Technological advancements in sealing methods, including gel-filled and heat-shrink systems, provide superior moisture protection and ease of installation and maintenance. These innovations help minimize maintenance requirements while ensuring that the closures remain effective for years.
3. Automation for Precision
Automation plays a key role in ensuring the high accuracy and reliability of our joint closures. Automated tools streamline the process of splicing and installation, improving the consistency of results and reducing the potential for human error.
Identifying and Addressing Joint Closure Issues
Sign of Wear | Recommended Action |
---|---|
Visible corrosion | Inspect thoroughly and consider replacement |
Cracks or deformation | Replace immediately to maintain integrity |
Water ingress | Assess damage and replace if necessary |
Brittle or peeling seals | Replace seals or the entire closure if faulty |
Conclusion
In the world of fiber optics, joint closures are a critical, yet often overlooked, component. They provide the necessary protection and stability to ensure the uninterrupted performance of fiber optic cables, safeguarding the integrity of signals and extending the longevity of networks. As the demand for high-speed, reliable communication grows, the role of joint closures will only become more significant.
Whether you're installing fiber optics for 5G, military communications, or any other application, investing in high-quality joint closures is essential. By choosing the right closure for your network, you ensure that your infrastructure remains secure, efficient, and ready to meet the future demands of the digital world.